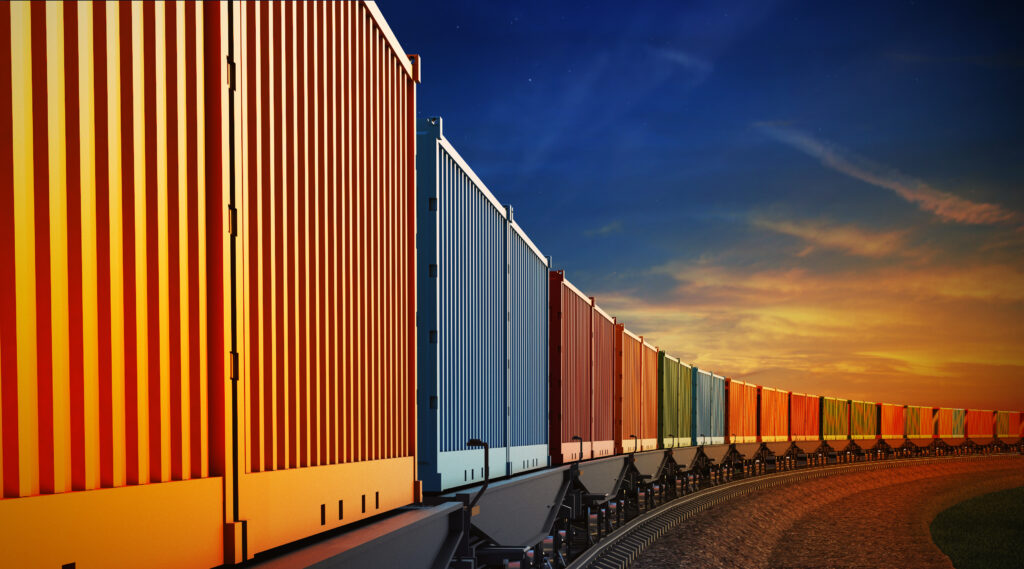
Lösungen:
Prozessautomatisierung
Branchen:
Eisenbahnwesen
[EN] Digitalizing Wagon Repair Verification
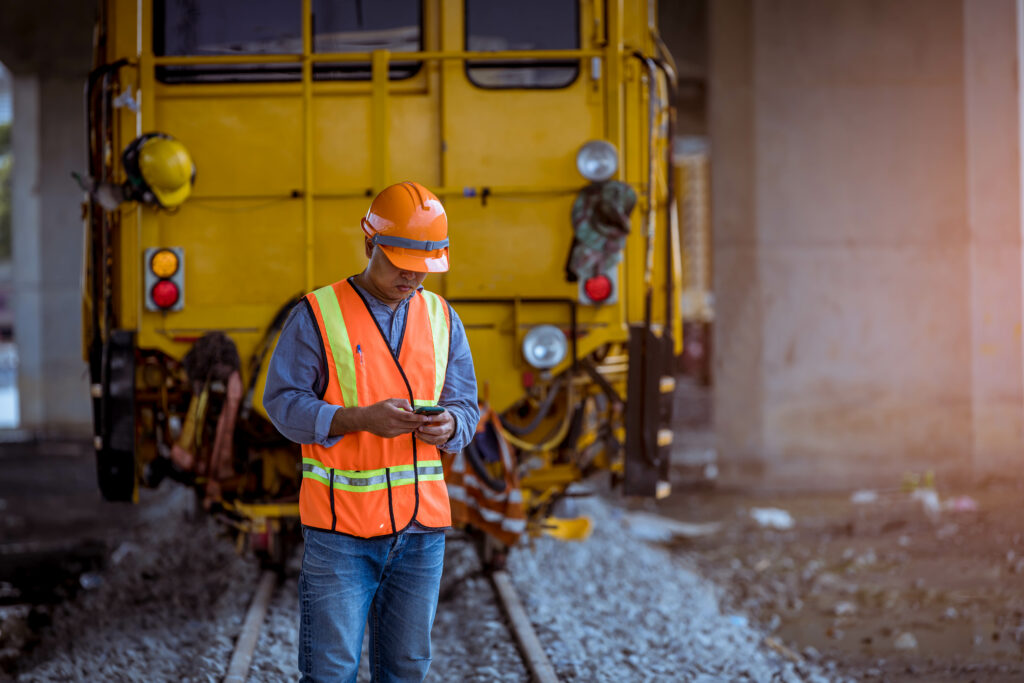
Die Herausforderung
GATX Rail Europe is an American company that rents out one of the largest fleets of rolling train stock in the world. Due to the size and nature of the business, thousands of documents are handled on a daily basis – primarily from workshops and the wider repair process for rolling stock.
Around 85% of these documents were being handled and exchanged manually – and off-the-shelf products had failed to successfully digitalize this process. Since the company had already been working with Univio, they decided to pursue a custom, dedicated solution that gave them complete control over the entire operation.
- Any solution needed to integrate with the company’s existing ERP.
- Data from repairs needed to be automatically verified so that the successful repair would be confirmed across the system.
- The solution needed to work on desktop, app and tablet devices.
- It would also be used by people on-site, often with heavy workwear (such as gloves) that needed to be accounted for in the usability and design.
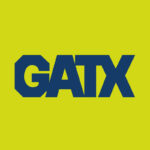
Die Lösung
- Data is stored in databases in the Cloud to optimize costs.
- Every wagon can have as many as 50 subassemblies, all of which need a virtual ID.
- A custom PWA is used to collect information from both desktops and workers on the floor with tablets.
- Report verification checks for validation and automates the process.
- As an end to end (E2E) solution, we included a complete SLA for 24/7 maintenance.
Das Ergebnis
Was wir gelernt haben
Before we began development, it was important for us to understand GATX Rail Europe’s business logic and the wider industry domain as a whole. To truly make the solution work, we learned the process behind their operations, the technical data required, the industry regulations needed to be met and how the highly-specific validation process itself should work.
Thanks to our close cooperation with GATX Rail Europe, who were more than happy to teach us these vital factors, we were able to build a complete E2E solution that, from the very start, was designed with their specific needs in mind. Throughout the project, the continued commitment of the Product Owner ensured the solution always met both their expectations and wider industry requirements.
Die Technologien
/ Hinter den Lösungen
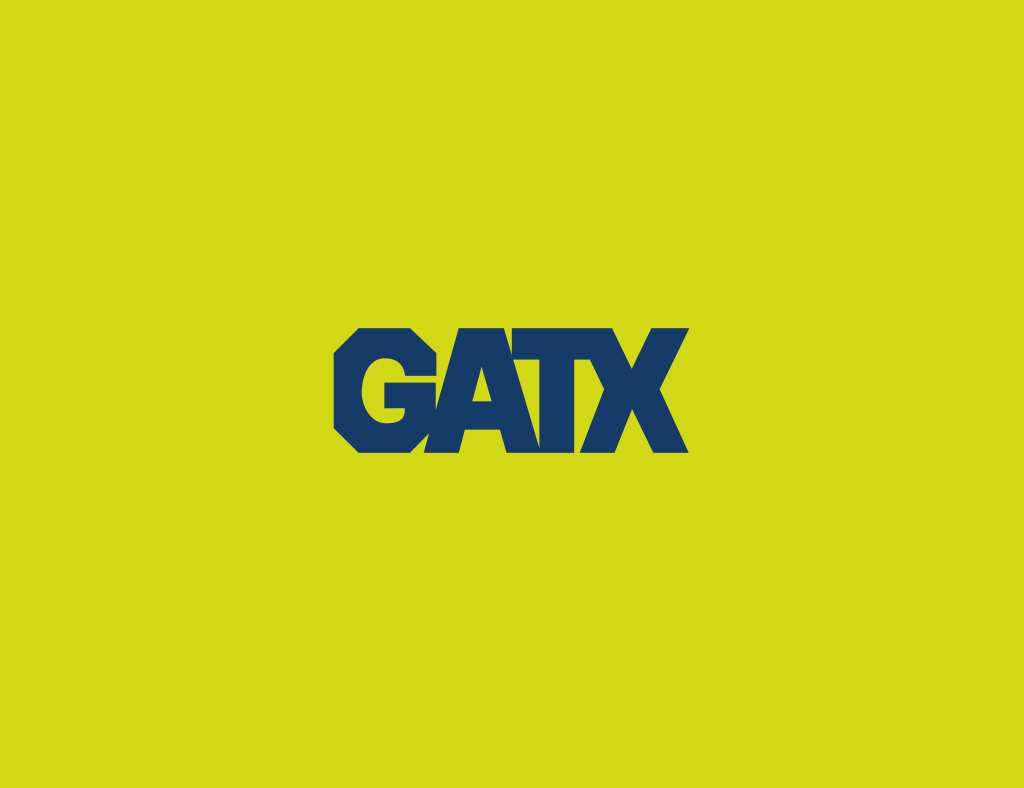
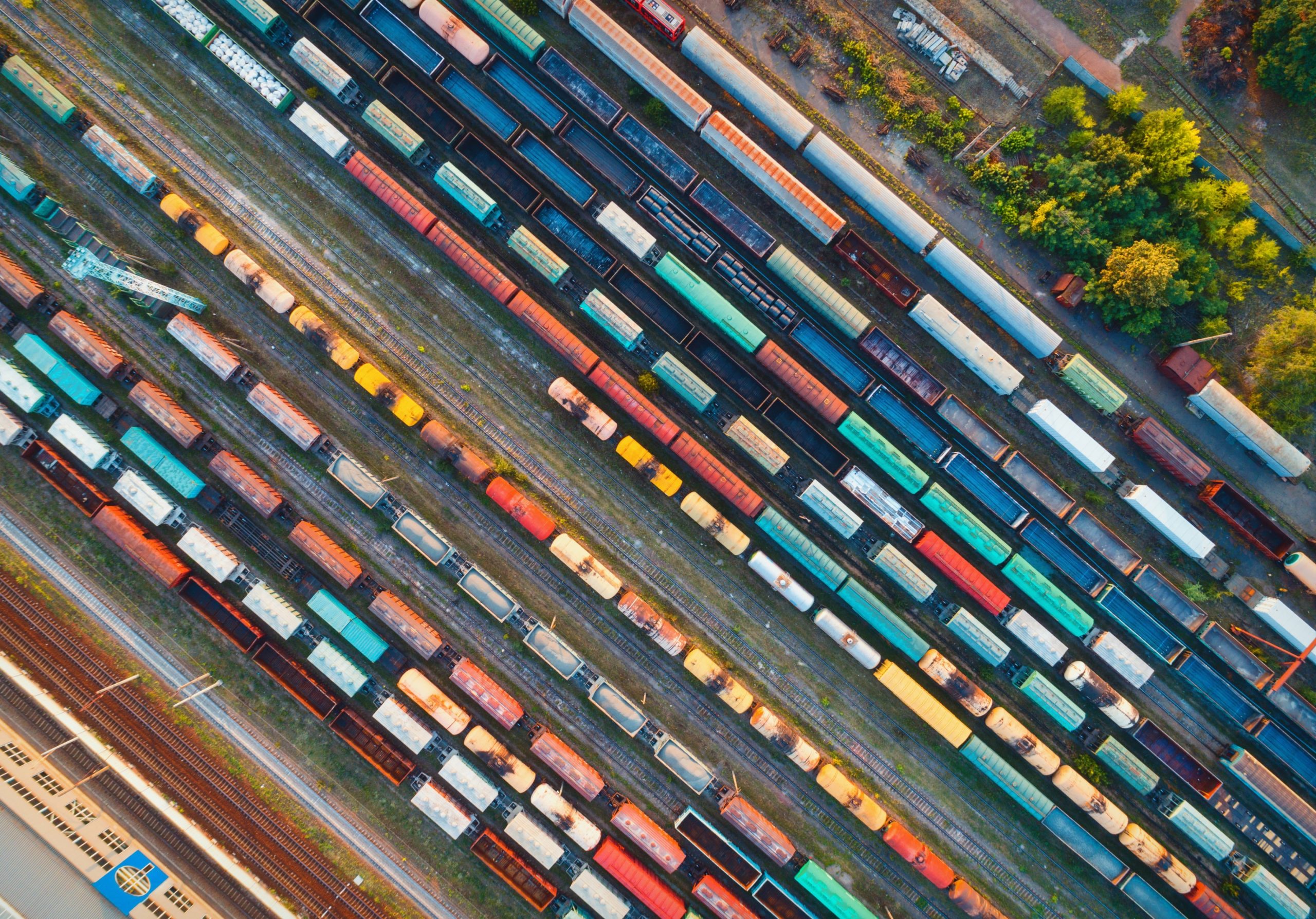
Migration des Radsatzmoduls auf ein zentrales Webportal
Nach der Implementierung des zentralisierten Shop-Portals haben wir GATX dabei geholfen, zusätzliche Schlüsselvorgänge zu übernehmen und so die Effizi