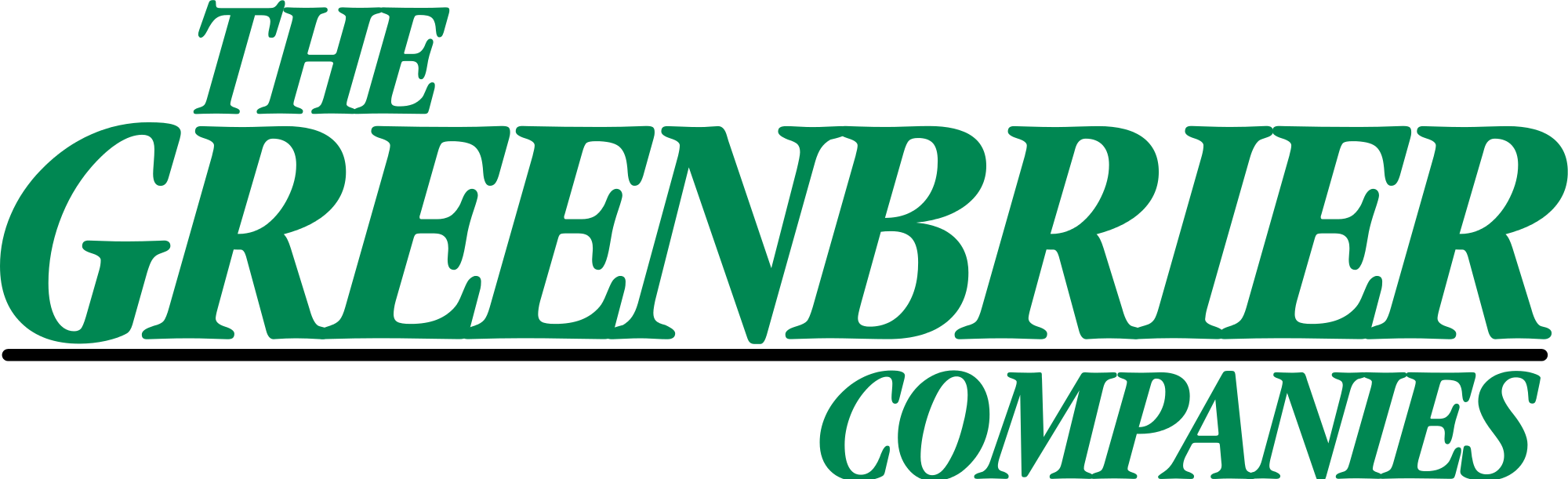
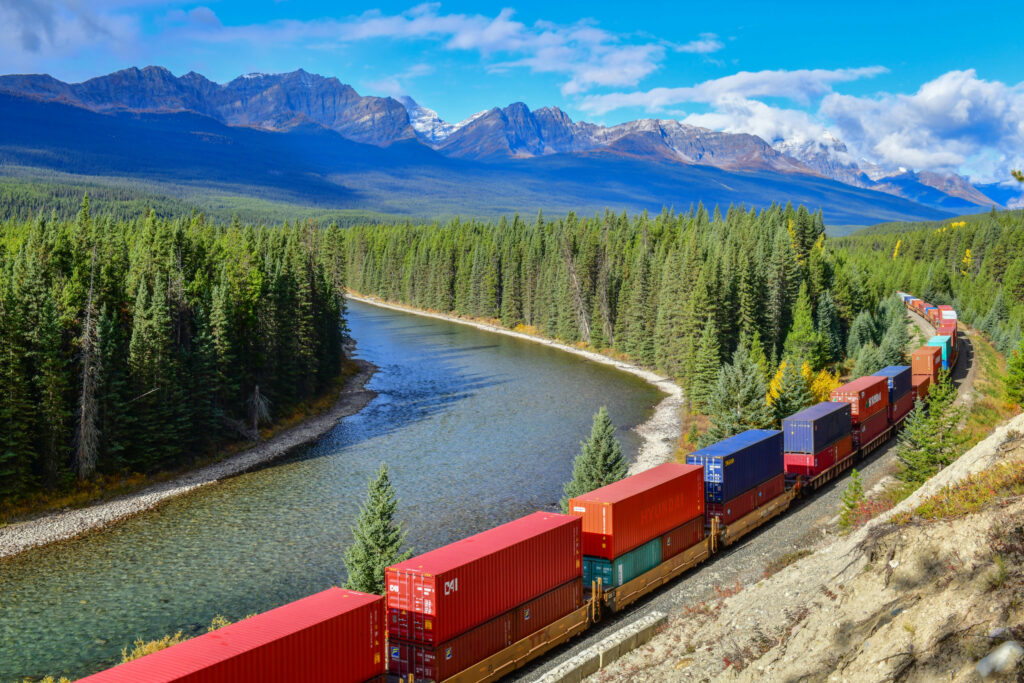
Solution:
Web Development
Industry:
Rail
ECM System for the Siarkopol Railway Transport Plant
Better process management
<process.simplified>
Improvement of repair processes
<time.saved>
Effective data management
<efficiency.improved>
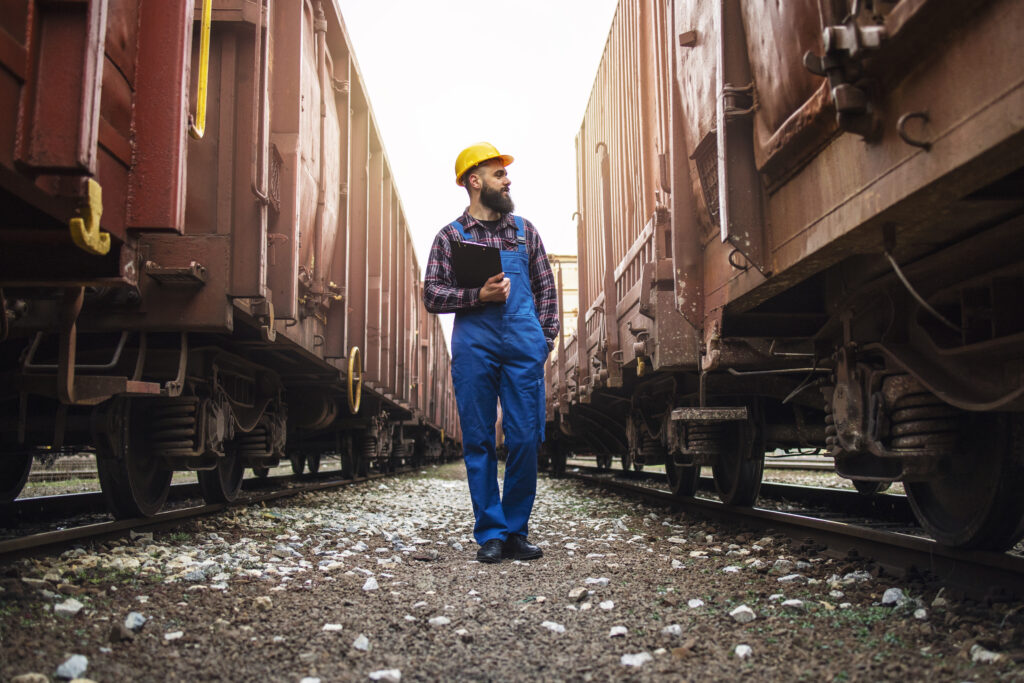
The Challenge
For this project, we needed to create a system supporting digital transformation at Siarkopol, which is part of the international group Greenbrier. We’ve helped digitize one of the company’s key areas.
We built a solution that allows for efficient management of repair processes and the leasing of rolling stock. The company’s own rolling stock consists of 350 traction units, which are maintained by a 30-person team.
- The main need we defined was to support and improve the management of processes of maintenance and lease of railway vehicles.
- An important aspect of the implementation was to enable the registration and recording of rolling stock maintenance activities and keeping a list of components and measuring instruments, including in terms of their rental.
- Another significant functionality was the automatic creation of schedules and distribution of tasks among employees. It was also important to provide users with information on current issues and the progress of repair work.
- Given the scope and scale of the company's operations, another essential element of the implementation was the integration of multiple data sources about carriages and ensuring easy access to the documentation and history of individual rolling stock elements.
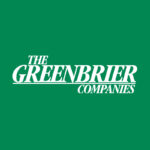
The Solution
- As part of the digital transformation, we built and implemented the solution using proven Microsoft technologies.
- Registers and reports – Several data registers were created as part of the system. The most important is the electronic list of wagons, components and tools. It contains their usage history, repair schedules and forecasts as well as full technical documentation.
- The system allows the user to register leases contracted by the company and provides the capacity to generate integrated reports for internal and external use.
- It also supports company employees in the daily maintenance of their own and other entities’ rolling stock. It allows them to record information about activities such as inspections and repairs in accordance with applicable maintenance documentation.
- Forecasting and managing the repair process – The tool allows users to create repair forecasts based on a schedule, as well as to generate to-do lists, and work and tool cards.
The Result
Better process management
Easier access to documentation.
<process.simplified>
Time saved
Creation of registers reduces the time needed for the management of repairs as well as rolling stock lease.
<operations.optimized>
Increased resource control
Tools for organizing work and defining schedules support the team in meeting deadlines.
<work.optimized>
Improvement of repair processes
The possibility of creating task lists, their system distribution and the option to monitor the progress of work accelerate the renovation of rolling stock.
<time.saved>
Effective data management
The system allows you to register, record and search for information about repair work and wagon leases.
<efficiency.improved>